Air New Zealand looks to hit 'print' on metal aircraft parts
09 August, 2018
3 min read
By joining our newsletter, you agree to our Privacy Policy
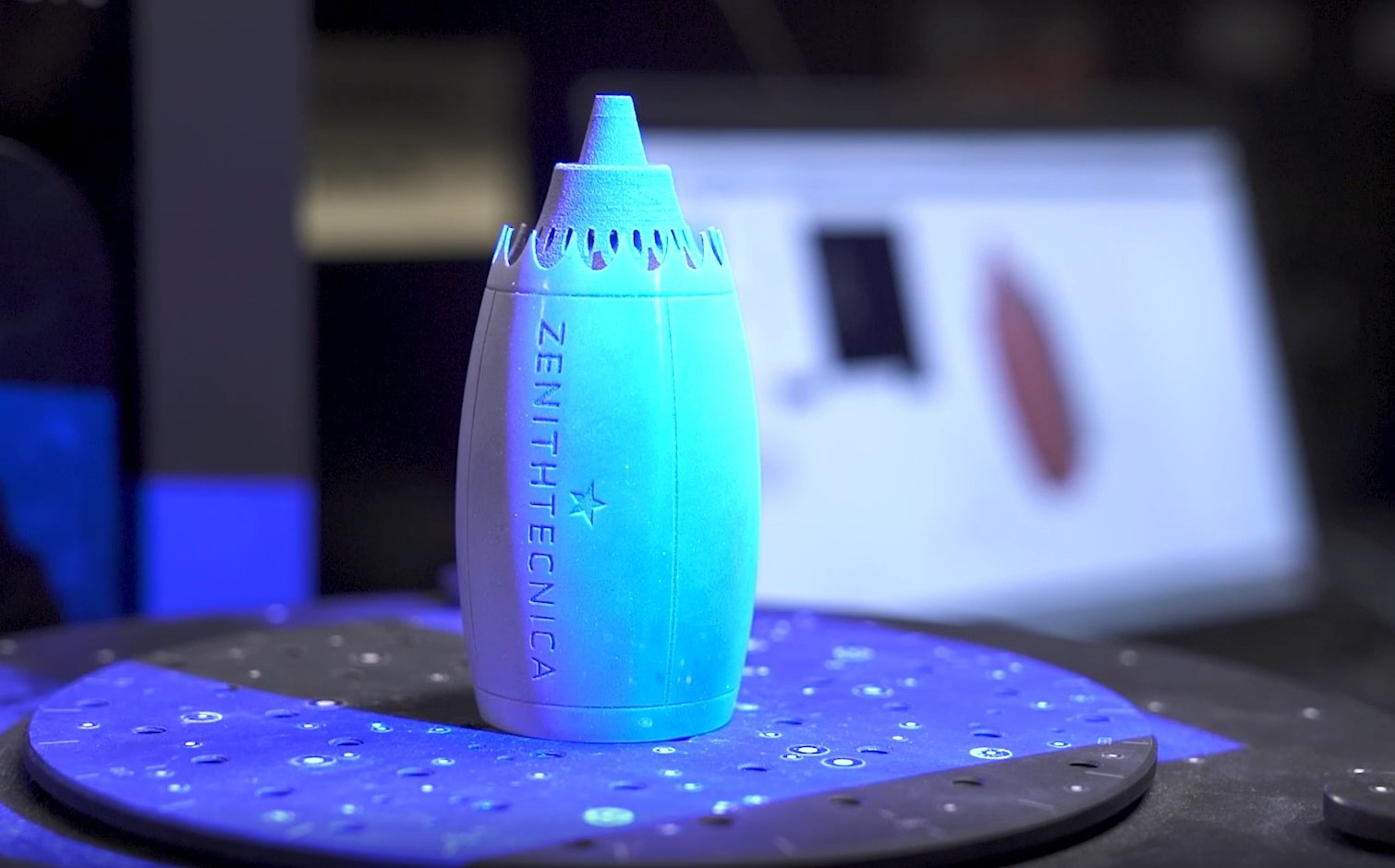
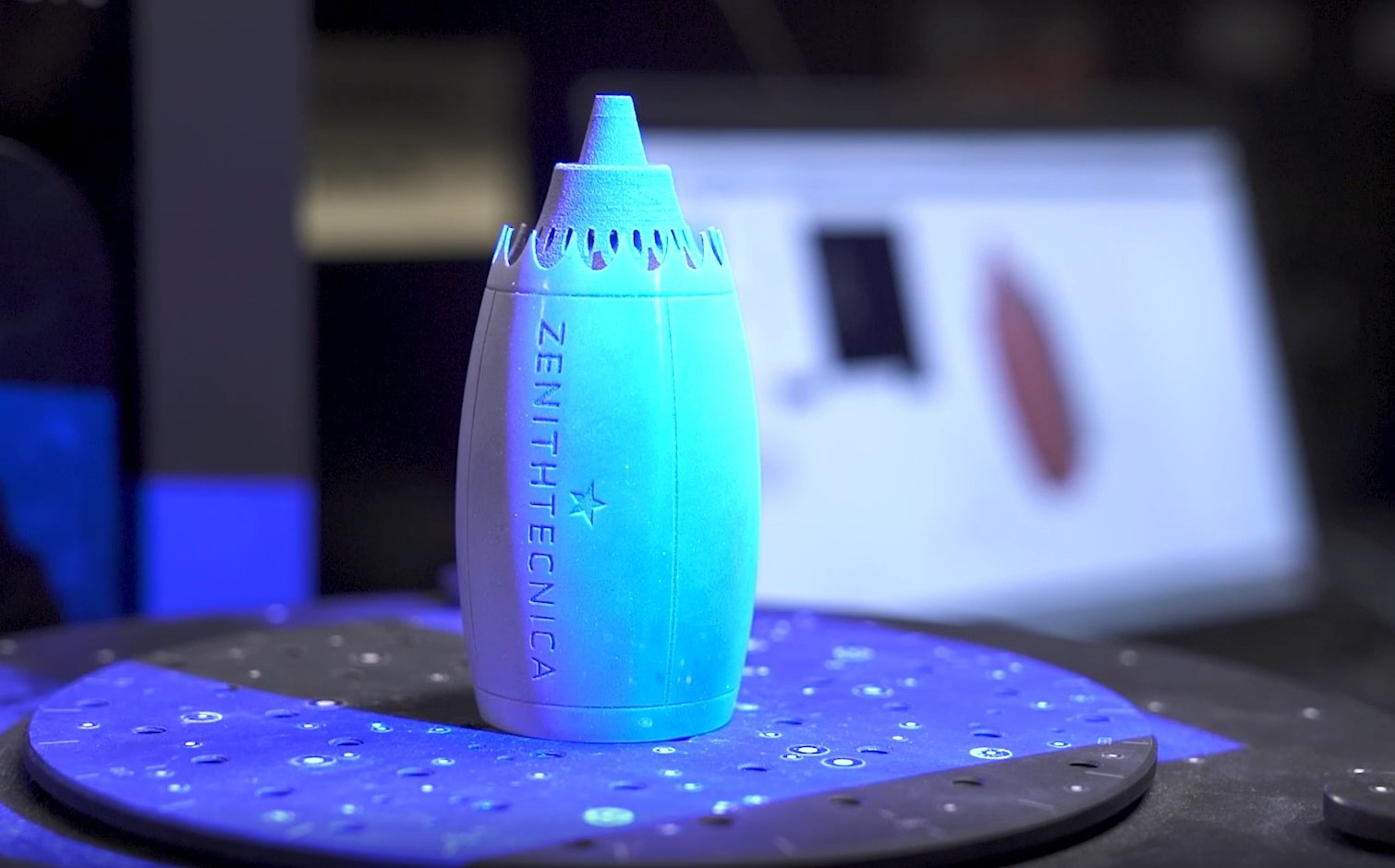
Air New Zealand is looking at how it may be able to save time and money by using 3D printed metal parts in its aircraft and tools.
It has joined forces with New Zealand company Zenith Tecnica, which specializes in the design and manufacture of 3D titanium and other metal parts using a technology called electron beam melting.
READ: Air New Zealand joins forces with JetBlue to foster travel innovation.
The technology is designed by GE Additive company ARCAM EBM and uses a powerful electron beam to melt metal powder in a vacuum. A part is then built up layer-by-layer, a process also known as additive manufacturing, using computer-aided design.
There has been increasing interest throughout the aviation industry in 3D printing technology because of the dual advantages of cost savings and the ability to more quickly produce complicated parts.
The process reduces wastage and the need to hold big inventories, allowing parts to be made according to demand and made available where they’re needed.
Printed parts are already used in aircraft cabins as well as in areas such as auxiliary power units and engines.
US manufacturer Boeing earlier this week announced its HorizonX venture fund had invested in Digital Alloys, a US-based company developing high-speed, multi-metal additive manufacturing systems that produce 3D-printed parts.
Boeing said it already had more than 60,000 3D-printed parts flying on space, commercial and defense products.
Air New Zealand’s foray into 3D printing began in 2016 and it now produces items such as improved parts for inflight entertainment screens.
The latest investment is part of a strategy that includes work with universities and partners such as aircraft maintenance company ST Engineering Aerospace to produce advanced parts.
“While we are in the initial stages of working with these companies on 3D printing, so far, we have printed prototype metal framing for our Business Premier cabin, to quickly test new concepts and ideas and we have also made novelty wine aerators,’’ Air New Zealand chief operations officer Bruce Parton said.
“While the aerators, made to look like replica aircraft engines, are a bit of fun we’re really excited by the possibility they represent as 3D printing is both cost and space effective.
“Aircraft interiors are made up of tens of thousands of parts, and the ability to 3D print on demand lightweight parts we only require a small number of, rather than rely on traditional manufacturing methods is of huge benefit to our business, without compromising safety, strength or durability.”
Zenith Tecnica managing director Martyn Newby said the Air New Zealand partnership was a good project to demonstrate the strength, versatility and utility of titanium 3D printed parts for aircraft applications.
The company already makes parts for a range of applications, including marine, industrial, medical and sporting uses. It also produces parts for satellites and is hoping the Air New Zealand partnership will help it open a new market in the aviation industry.
“We are in a very good position to support the local adoption of 3D printing for aviation applications and welcome Air New Zealand’s enthusiasm to embrace this emerging technology and help take it to the mainstream,” he said.
Get the latest news and updates straight to your inbox
No spam, no hassle, no fuss, just airline news direct to you.
By joining our newsletter, you agree to our Privacy Policy
Find us on social media
Comments
No comments yet, be the first to write one.