Airbus uses first 3D printed part in A350 engine pylon.
14 September, 2017
2 min read
By joining our newsletter, you agree to our Privacy Policy
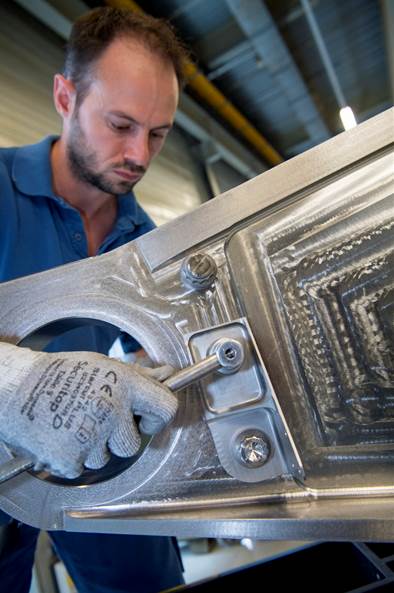
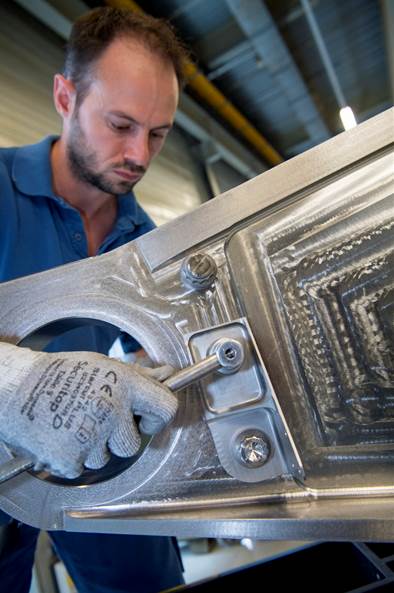
Airbus has for the first time installed in a production aircraft a titanium bracket produced by a 3D printing process.
The bracket is part of the engine pylon, the junction between the wings and the engines, on an A350 XWB.
The European manufacturer said the move was a first step towards qualification of more complex 3D-printed parts on production aircraft.
Additive-layer manufacturing, as 3D Printing is also known, uses a fine base powder such as aluminium, titanium, stainless steel of plastics to build a component by repeatedly adding thin layers.
It allows the construction of complex, computer-designed components that would be difficult to build using traditional manufacturing.
Airbus has been looking at the technology for a number of years and already uses 3D printed parts on some A320neo and A350 aircraft, including metal cabin brackets and bleed pipes.
The parts can be up to 70 per cent cheaper as well as much quicker to produce and Airbus officials are looking to harness a technology they have described as a potential game changer for design and manufacturing.
The technology has the potential to reduce the material wasted when milling parts as well as cut down the shipping of materials to multiple sites producing components.
It also offers a simpler way to produce complex assemblies and allows prototype parts to be made to ensure they work correctly or fit together properly with other components.
The manufacturer has predicted the number of printed parts could number in the thousands in coming years.
But first regulators need to be certify the parts and be convinced they are as robust as those made by traditional means when used in areas subject to structural stress.
Airbus rival Boeing announced earlier this year it would using 3D-printed titanium parts in the construction of its 787 Dreamliner jet airliner.
These are the were the first 3D-printed structural components to be approved by the Federal Aviation Administration and manufacturer Norsk Titanium predicted the shift to the technology could eventually save the US plane maker up to $3 million in construction costs per jet.
Next Article
2 min read
Qantas triples profit but misses mark
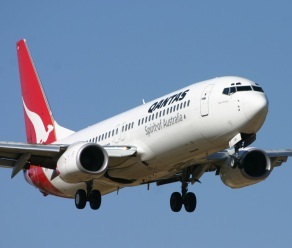
Get the latest news and updates straight to your inbox
No spam, no hassle, no fuss, just airline news direct to you.
By joining our newsletter, you agree to our Privacy Policy
Find us on social media
Comments
No comments yet, be the first to write one.